It began in mid-2013 with the search for a suitable software solution. The requirements defined by the legislator could no longer be met manually in the classic way via a stock ledger in paper form.
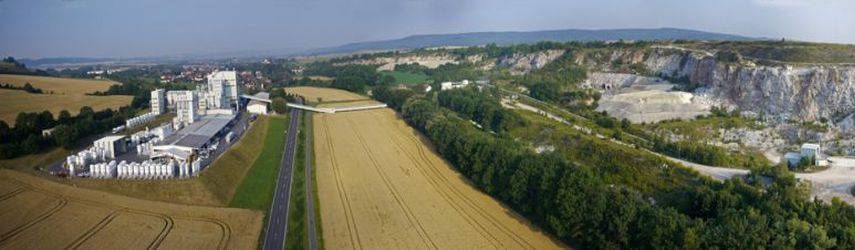
Setting Common Requirements
There had to be an EDP solution that would meet the requirements of both open pit and mining operations. In joint meetings, the following list of requirements for the electronic stock ledger and the required hardware was defined:
- Compliance with the EU Labeling Directive
- Internet connection not necessary
- It is easy to operate
- Clear and easy to read interface
- Low training effort
- Suitable hardware for use in explosives storage and handling of detonators
- The greatest possible protection of data
Furthermore, the solution should integrate into the workflow in such a way that no additional work steps are required, e.g. at the end of the day by reworking the data collected during the day (e.g. by synchronizing the devices).
Development Partnership
“We had been looking around intensively on the market for a solution for quite a while, but hadn’t found anything suitable,” says Anke Adler, IT manager at maxit Baustoffe GmbH. This gave rise to the idea of entering into a development partnership with the company Ontaris GmbH & Co. KG from Wuppertal, with whom they have been working together very successfully for a long time. The goal was to develop a solution that would meet the previously defined requirements.Together, the work processes were analyzed in detail, starting with the order, through delivery, storage and consumption. The equipment to be used was selected and tested together and the program interface was defined. The result was a program that works on a robust 9”-TabletPC with a handy scanner, connected via Bluetooth.
Dialogue with the Authorities
Since the review of the implementation of the labeling directive is the responsibility of the individual state authorities, direct contact at an early stage was important. “We have a very good relationship with our responsible supervisory authority and discussed the implementation with them at an early stage,” says Wolfram Lisker, Head of Mining at maxit Baustoffwerke GmbH.
The First Practical Test
At the beginning of April the time had come. For the first time, the delivery of explosives was to be received and accounted for using the new system. The XML file from the supplier containing all IDs for the entire shipment was delivered by email the day before. The next day, when the delivery of the explosive took place, it was used for the electronic receipt of goods and to carry out the sampling.
“It was a very exciting moment to work with the system for the first time. Everything we had thought about beforehand now had to prove itself in practice,” says Wolfram Lisker; But before the time came, the first hurdle arose. The XML file from the manufacturer could not be loaded with the software. The structure did not yet comply with the FEEM standard. During the analysis of the file by the Ontaris team, the cause was quickly found and corrected in such a way that the goods acceptance could be carried out the next morning after all.
Direct Dialog with the Manufacturer
“Up to that point, the manufacturers were in the situation where they could generate the XML files, but they didn’t have a buyer for them yet. Therefore, it was not surprising that there were still a few things to correct,” is how Martin Schüßler, CEO of Ontaris, sums it up. Due to the direct communication of the developers of Ontaris with the responsible developers of the manufacturers, the errors could be corrected quickly and unbureaucratically, so that future deliveries can be booked without problems with the electronic stock book.
Handling Hrdware and Software
“Before the development of the software began, we sat down with a number of friendly companies and together considered which devices would cause us the least disruption when working in the quarry. We had all the devices in our hands once and then jointly decided on the solution with a small handheld scanner,” Wolfram Lisker summarizes. “This has been positively confirmed in the first practical test;

The tablet PC could be placed on a stack of boxes while working, and the handheld scanner quickly disappeared into your pocket when you needed both hands. Furthermore, the entire software can be operated with the finger. No mouse or any other additional tool is needed.
Authentication by Badge
An important issue that had to be clarified with the representatives of the authorities was how to deal with the electronic stock ledger and the legal requirement for the type of record keeping. An exemption is no longer needed for electronic record keeping. For the authentication of the warehouse manager, a PIN code is enough to protect access to the software from unauthorized access.
For the issuance, it was decided to use a badge, which is given to each employee authorized to blast. When the storekeeper issues the explosives to another person authorized to blast, the latter shall show his blasting identification card. A data matrix code is applied to this, which is read in with the hand-held scanner and thus uniquely identifies the person authorized to blast.
This is automatically noted in the Explosives Stock Book and can be verified during a subsequent audit. Thus, the signature of the user can be omitted.
The Stock Book
The used concept of working with a self-sufficient tablet PC automatically complies with the regulatory requirements that every movement in the explosives storage is immediately and fully automatically written into the storage book. Completion of the stock ledger at the end of the day on the PC in the operations office is therefore no longer necessary.
Conclusion
“The first practice run reassured us a lot,” says Wolfram Lisker. “It was clear that there was still a bit of a hitch in one place or another, but that’s just the finishing touches now.” The feared extreme additional effort due to the implementation of the labeling directive has not materialized. On the contrary: when recording the data with our new system, we can achieve considerable time savings compared to the previous manual management of the stock ledger.
Mrs. Anke Adler is also very satisfied: “For us it was the right decision to go the way together with Ontaris. In many joint meetings and workshops, in cooperation also with other companies, a simple, clear system was created that fully complies with the legal requirements – We are ready for April 01, 2015!”