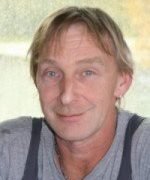
“I am extremely satisfied with the Ontaris system. Overall, the time spent is less, the whole thing runs easier and faster. I don’t want the green book back.”
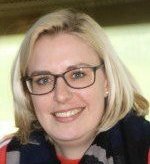
“Due to the situation at the explosives manufacturers, an introductory phase was not feasible for us, even if it had been planned in advance. This was mainly due to the electronic delivery bills, which were not available across the board.”
It is 7 o’clock in the morning. A beautiful autumn day announces itself. A truck with a delivery of explosives is parked in the yard. The explosives will be unloaded by the forklift and transferred to the bucket of the wheel loader, which will then take them to the blasting site.
Incoming Goods: Simple and Fast
Alfons Planken, the blasting foreman in charge at SHI (Sauerländer Hartkalkstein-Industrie GmbH) in Bad Wünnenberg, is already checking the delivery while this is happening. Using the delivery note, he goes through the individual items and checks them off. This is routine; for years, every delivery has been received and checked by him in this way. The fact that he now takes a robust tablet computer with a small scanner and uses it to check the goods has been new since April. After 10-15 scans, he releases the goods for transfer to the blasting site, presses the tablet computer display and books the explosives into the electronic explosives stock book.
The New EU Directive
This new technology made its way into the entire MHI (Mitteldeutsche Hartstein-Industrie Group) group of companies six months ago; a few months before, on 5. April 2015, the Europe-wide directive came into force. Since then, any company handling explosives and detonators is required to ensure full traceability of the item used. Alfons Planken also knows that this was not very positively received in the industry at first, but was rather fraught with many fears. “There was no opportunity to become familiar with the new system before it was introduced, there was no time to practice because the explosives manufacturers in particular were not ready.”
Since April 5, 2013, all manufacturers of explosives are required to mark each individual detonator, cartridge or detonating cord with a unique number. It was agreed that this marking, in addition to the numerical representation, would be made via a DataMatrix code on each individual article. On April 5, 2015, the traceability obligation then also came into force for consumers. As a result, all individual numbers must be documented at goods receipt and accordingly which ones are consumed when.
To make the whole thing practical, the European explosives manufacturers stipulated that each delivery should be accompanied by a digital delivery bill, in the form of an XML file, containing all the individual identification numbers of the explosives delivered.
Everyone is Waiting, but for What?
Before the directive came into force in April 2015, the topic “Track and Trace of Explosives” was discussed very controversially. It has always been a main component at meetings and seminars since 2013. Only the implementation did not get off the ground. Time passed without producing any tangible results. Manufacturers did not provide digital delivery bills because there were allegedly no users who wanted to receive this data with the delivery. Everyone waited. But on what?
Development of a Solution by Ontaris
At the end of 2013, the company Ontaris GmbH & Co. KG from Wuppertal, in close cooperation with several quarries, mines and explosives dealers, started to redevelop a system that is easy to use and optimally adapted to the application case and looked for companies from their side to gather initial practical experience. “Everything was new. The blasters in the companies were not used to working with computers. In addition, the processes of how the digital delivery bill would be transmitted by the supplier were completely unclear. You had the feeling that no one wanted to take the first step,” says Martin Schüßler, Managing Director of Ontaris GmbH.
Introduction at MHI Group
At the same time, MHI addressed the new directive at an early stage within the group of companies and looked around for a suitable provider for the implementation. Thus, in the summer of 2014, the first talks with the company Ontaris took place.
MHI was quickly convinced by the Ontaris Explosives Stock Book. The blasting authorities of the individual plants recommended the solution for the MHI Group, so that the implementation could take place at the beginning of 2015. Unfortunately, at that time the explosives manufacturers were not yet ready with their IT and the training of the new processes so that they could regularly and reliably add the digital delivery bills to the deliveries. “It took a lot of energy, and the blasting operators barely had time to familiarize themselves with the new system before it had to be implemented in April 2015,” says Katharina Hermsen, executive assistant for technology at the MHI Group.
Back Posting of Unspent Explosives
Meanwhile, on the blasting site, the blasting is prepared so far. The holes are filled, the detonators wired. The unneeded explosives will be returned to the supplier’s truck. There, Alfons Planken scans the cartons and some detonators back to the supplier using the Ontaris system. Clicking on the stock control immediately gives him the certainty that he has made all the bookings correctly. The stock level shows an empty warehouse and the stock movement contains all performed actions.
Conclusion
Martin Schüßler knows that in practice there are always things that are not regulated by law. “Nowhere is it written what I have to do if I have to take explosives from the blasting site back to my warehouse, or return them to the supplier if the flag with the barcode has become soiled or lost. We have found a very simple, pragmatic solution for these cases. We have continued to develop our system over the last few months so that our customers can work even better with it.”
Alfons Planken also draws a positive conclusion from the first six months of practical implementation with the help of the tablet, after initially being very skeptical: “I am extremely satisfied with the Ontaris system. Overall, the time required is less, the whole thing runs easier and faster. I don’t want the green book back.”